L’IRT SystemX a développé une chaîne numérique d’outils et de méthodes innovantes, capable de simuler un procédé de fabrication additive de type LMD (Laser Metal Deposition). Cette simulation a pour objectif d’évaluer différentes stratégies de réalisation en fonction de la géométrie de la pièce, afin d’optimiser le procédé en production en matière de qualité et de délais.
Mise au point en collaboration avec DP Research Institute (DPRI), l’ENS Paris-Saclay, l’ENISE (École d’ingénieurs en Génie Mécanique, Civil, Physique – École Centrale de Lyon), Safran et SPRING Technologies, cette solution logicielle assure une simulation topologique de la pièce intégrant les données cinématiques simulées (c’est-à-dire la vitesse et la position de la buse en fonction du temps). Elle repose sur quatre briques logicielles :
- une brique de simulation de dépôt de matière,
- une brique de simulation cinématique du comportement machine,
- une brique de gestion des collisions,
- et une brique d’optimisation des trajectoires.
Le démonstrateur a été exploité par Safran afin de traiter un cas d’usage de fabrication d’une pièce. Les résultats obtenus ont permis de valider les critères d’évaluation des différentes stratégies de fabrication.
Ce démonstrateur apporte des avancées significatives dans le domaine de la fabrication additive. Il rend possible la simulation de la géométrie résultant du dépôt de matière, la prédiction réaliste de la vitesse d’avance de la buse (et donc du temps de fabrication) et la gestion des collisions pour optimiser les trajectoires. L’objectif est de définir et de valider une stratégie de fabrication en production.
Xavier Lorang, Chef de projet et Responsable de la thématique Fabrication additive, IRT SystemX
Interview
Xavier Lorang
Chef de projet et Responsable de la thématique Fabrication additive, IRT SystemX
Comment s’est déroulée votre collaboration avec l’IRT SystemX ?
Mis à disposition à l’IRT SystemX pendant trois ans, j’ai eu l’opportunité de monter trois projets de R&D dans le domaine de la fabrication additive. Le modèle de l’institut nous permet d’avancer dans la réalisation de prototypes numériques. L’équipe transverse Software & DevOps nous accompagne pour développer nos démonstrateurs et partager nos résultats, ce qu’on ne pourrait pas faire dans un laboratoire de recherche.
Que vous a apporté cette expérience ?
Mon passage à SystemX m’a beaucoup apporté dans le domaine du montage de projets et m’a permis de découvrir d’autres enjeux scientifiques et technologiques, tels que l’internet de confiance, qui s’applique aussi en fabrication additive. J’ai pu y partager mes compétences en fabrication additive et en définition numérique de processus de fabrication. Ajoutées à l’expertise des partenaires industriels et académiques, elles ont bénéficié à l’IRT qui excelle pour accompagner la transformation numérique de l’industrie. Nous avons fait avancer les recherches dans le domaine de manière significative comme en attestent le démonstrateur CDF (Conception des Directives de Fabrication) et les projets DSL (Durabilité des Structures Lattices) et WAS (Wire Additive manufacturing process Simulation).
Focus
Dans le domaine de l’ingénierie pour l’industrie du futur, l’IRT SystemX s’est également intéressé, en collaboration avec Safran, à l’étude de l’impact des variabilités liées au procédé de fabrication sur l’état de la matière, la résistance mécanique et la durée de vie des structures fabriquées.
Interview
Oana Ciobanu
Ingénieur méthodes numériques avancées pour la Fabrication additive, Safran
Quelle place occupe le domaine de la fabrication additive au sein du groupe Safran ?
La fabrication additive chez Safran est dédiée au développement et à la livraison de produits compétitifs et innovants. L’objectif est de favoriser la création de valeur au service des clients des sociétés du groupe.
Que retenez-vous de votre collaboration avec l’IRT SystemX ?
L’IRT SystemX a accompagné Safran dans un premier projet collaboratif, impliquant également l’IRT Saint Exupéry et d’autres acteurs industriels et académiques, autour de la fabrication additive. Dès les premiers échanges, une collaboration fluide a été construite. L’institut a porté un grand intérêt au sujet et a démontré une compréhension avancée du besoin industriel associé. SystemX a pris en charge le pilotage du projet. Ce dernier a permis le développement de méthodologies et d’outils numériques destinés à la conception des pièces issues de fabrication additive par fusion sur lit de poudre et à l’étude de leur comportement. Les connaissances de l’état de l’art de l’IRT SystemX ont été mises à profit dans l’étude de l’impact des dispersions de fabrication sur la tenue en service des pièces. Un objectif de transfert des connaissances s’est remarqué dans tout développement numérique, regroupé dans une plateforme performante, rapide et simple d’utilisation, disponible dans l’infrastructure Safran.
Calcul scientifique et optimisation
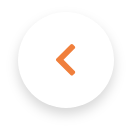
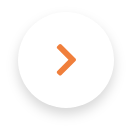