IRT SystemX has developed a digital chain of innovative tools and methods capable of simulating a Laser Metal Deposition (LMD) additive manufacturing process. The aim of the simulation is to evaluate different creation strategies based on the geometry of the part, in order to optimise the production process in terms both of time and quality.
Developed in collaboration with DP Research Institute (DPRI), ENS Paris-Saclay, ENISE (Engineering school of the École Centrale de Lyon), Safran and SPRING Technologies, this software solution provides a topological simulation of the part that integrates simulated kinematic data, i.e. the speed and position of the nozzle according to time. It relies on four software blocks:
• a simulation block for material deposition,
• a kinematic simulation block for the behaviour of the machine,
• a block for collision management,
• and a brick for the optimisation of flow paths.
Safran has used the demonstrator in a use case for manufacturing a part. Thanks to the results, they were able to validate the evaluation criteria of different manufacturing strategies.
This demonstrator provides significant advances in the field of additive manufacturing. Thanks to the simulator, we can simulate the geometry resulting from deposition, realistically predict the feed rate of the nozzle (and thus manufacturing times), and manage collisions to optimise the flow path. The aim is to define and validate a manufacturing strategy during production.
Xavier Lorang, Project Manager and Head of Additive Manufacturing, IRT SystemX
Interview
Xavier Lorang
Chef de projet et Responsable de la thématique Fabrication additive, IRT SystemX
What can you tell us about your collaboration with IRT SystemX?
Over the three years I spent at IRT SystemX, I launched three additive manufacturing R&D projects. The model of the institute enables us to move forward in the creation of digital prototypes. The cross-disciplinary Software & DevOps team supports us in the development of our demonstrators and helps us share our results, which would not be feasible in a research lab.
What did you gain from this experience?
My time at SystemX was very fruitful. I learned a lot about project management and about other scientific and technical issues, such as the internet of trust, which also applies to additive manufacturing. I was able to share my skills in additive manufacturing and in the digital definition of manufacturing processes. Added to the expertise of industrial and academic partners, IRT SystemX was able to leverage on these skills, as it excels in supporting the digital transformation of industry. We have been able to make significant progress in the field, as seen with our CDF demonstrator (Conception des Directives de Fabrication – Design Manufacturing Guidelines) and both our DSL (Durability of Lattice Structures) and WAS (Wire Additive manufacturing process Simulation) projects.
Focus
In the field of engineering for the industry of the future, IRT SystemX is also studying, in collaboration with Safran, how variability in the manufacturing process impacts the state of matter, mechanical resistance and the service life of manufactured structures.
Interview
Oana Ciobanu
Engineer, Advanced Digital Methods for Additive Manufacturing, Safran
What is the role of additive manufacturing within the Safran group?
At Safran, additive manufacturing helps to develop and deliver competitive, innovative products. The aim is to create value for the group’s customers.
What can you tell us about your collaboration with IRT SystemX?
IRT SystemX supported Safran in our first collaborative project around additive manufacturing that also included IRT Saint Exupéry along with other industrial and academic players. We established a smooth collaboration from our very first meetings. The Institute showed great interest in the subject and demonstrated a deep understanding of the resulting industrial need.
SystemX was in charge of piloting the project. The aim was to develop digital tools and methodologies to design parts for additive manufacturing using powder bed fusion and study their behaviour. Thanks to the knowledge of the IRT SystemX on the state-of-the-art, we were able to study the impact of manufacturing dispersions on the service life of parts. Knowledge transfer has been at the heart of all digital developments, brought together in a fast and easy to use high-performance platform available in Safran’s infrastructure.
Scientific computing and optimization
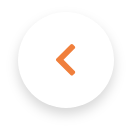
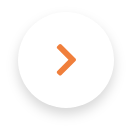